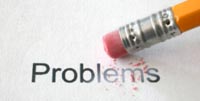
Industry Problem and Solution
This pages consists of the following sections in this order:
Industry OverviewEarthworks is a critical element of construction, and fills are a critical element of all shallow foundation infrastructure including environmental containment facilities. However, designers and builders do not get the controls they need from the geotechnical sector for soil construction. The geotechnical sector determines the engineering requirements of infrastructure fills, but inadvertently, no direct connection or control is provided for that in construction. The construction specs used are based entirely on assumptions, and actually conflict with construction. Consequently, earthen fills are the only element of infrastructure designed and built with assumptions, trial & error compromise, and no direct verification. This prevents builders from having control over performance, production, cost, and results.
“Fills are the only area of design and construction conducted by trial & error compromise - where the construction specs are always compromised, compaction standards are not achieved, design requirements are not met, and the builders do not have control over performance, cost, schedule, and results.”
The trial & error compromise is necessary to keep construction moving on all projects, and industry standards are not achieved as many believe. In fact, if the trial & error compromise is not conducted, construction could never be completed. This condition is the cause of the historic and unavoidable production vs. performance dilemma in construction - a perpetual vicious cycle with no end solution (illustrated below). The problem is so great it caused formation of the “intelligent compactor” industry long ago, with hundreds of millions of dollars invested now, and there is still no solution. This lack of control is a condition of all projects. The condition causes excessive construction costs, schedule delays, deficient soil construction, significant ground movement problems, excessive maintenance and repair costs, significant infrastructure damage, increasing construction claims, increasing/arduous construction guarantees imposed in contracts, and heavy litigation of the earth movement exclusions in CGL policies. ![]() Earthwork is the only area of construction where the constructor does not have full control over cost, schedule, performance and results. Contractors are continuously forced to meet testing controls that always conflict with the mechanical performance of their compactors. This is why all infrastructure fills must be built with trial & error compromise. These conditions cause the historical performance vs. production dilemma in construction, and the fundamental problem source persists. The dilemma in earthwork construction is illustrated in following graphic: ![]() ESOL resolves all of these problems and breaks the cycle by providing engineers and contractors with the controls they need without changing any of the process control methods the industry uses today. SolutionESOL fills these historical gaps between the geotechnical sector and the designers and builders in the industry. ESOL fills these gaps by removing the assumptions from the process controls without changing industry methods. This solution eliminates the trial & error compromise in construction, achieves industry standards with real-time control and direct-data verification, remedies the historic production problems, and remedies excessive damage, maintenance, and repair costs. Construction records demonstrate the best possible construction control and performance with direct data proof - the ultimate defense and liability protection record. ESOL also fills the shortfalls of “smart compactors.” See typical before and after project results. Construction CostsThe “big ticket” cost to owners is always the construction costs - not the engineering costs. Engineering is always a small percentage of project costs. Infrastructure projects are primarily composed of three construction material elements: concrete, steel, and soil. Only the soil fill elements are constructed with trial & error compromise. These trial & error exercises increase construction costs, jeopardize the concrete and steel built over the fills, and increase maintenance and repair costs. ESOL eliminates the compromise and construction risks, reduces construction costs, and removes the risks of very high construction costs - all without increasing engineering costs. The degree of cost savings for owners and constructors varies on all projects. The savings depends on the varying degrees of trial & error exercises to which one is comparing. A general range of ~15% to ~35% cost savings has been conservatively estimated based on source knowledge, construction surveys and estimates. An average of ~25% to 30% overall savings in earthen fill costs is considered a safe general range when no compromise is desired. The savings can be higher or lower depending on project circumstances. Cost savings are realized from many controls, including: - avoided trial & error exercises including reworks, reduced or eliminated needs for moisture change, expanded construction moisture ranges, expanded soil property ranges, real-time controls, and rapid control reports. ![]() Industry Compaction StandardsThough largely unrealized, the industry required compaction standards are essentially never achieved in cohesive fill construction. This condition is the primary source of the greatest problem in infrastructure: strength loss, saturation settlements and shrink-swell problems in founding fills. This condition is also the source of excessive permeabilities in environmental protection fills, barrier fills and structural fills. ESOL corrects this problem, without changing practice or any process control approach used today.
“Compaction is largely misunderstood in the industry, and ...”
![]()
“... fill construction is largely taken for granted.”
This condition is largely unrealized in the industry, though it is proven by direct data on every construction project. The conventional compaction standards specified for construction of cohesive fills are typically tied to optimum moisture content and maximum dry-density. The compaction standards always require a moisture range during compaction, which is tied to optimum moisture content. Usually, the compaction standards require a density range result after compaction also, which is tied to maximum dry-density. Typical examples of compaction standards include:
Most engineers understand the importance of achieving the compaction standards in construction. Most engineers understand most of the reasons why wet-of-optimum compaction is critically important. Many engineers understand the dangers of dry-of-optimum compaction. However, few engineers realize their compaction standards are not being achieved in construction. Few engineers realize that the beliefs and uses of lab compaction curves is the cause of this problem. This is the primary source of the greatest problem in infrastructure.
“Only by disregarding engineering standards, requirements, and objectives could ESOL's process control solutions be viewed as any sort of ‘change in practice’ ...”
The assumptions, beliefs and uses of lab compaction curves disable the process control methods we use in construction today. Many engineers assume that lab compaction test curves represent field compaction or a degree of field compaction. These are incorrect assumptions on many levels. In all ways, lab compaction is different than field compaction. These beliefs prevent our process control methods from achieving our compaction standards. The result in construction is trial & error compromise and adverse compaction - unintended and unrealized. In earthen fill construction today, it is virtually impossible for the moisture-density relations in lift compaction to match relations from lab compaction tests. It is also wrong to assume that compacted lift properties will ever match lab compacted properties, even when in the same moisture-density space. Assumptions and trial & error exercises are necessary though - on all lifts on all projects - in order to find a way to get some sort of fill construction done to some result. These trial & error exercises include “lab curve shopping”, “field data shopping”, new lab curves, parallel lab operations (for more curves to “shop”), false moistures after compaction, moisture adjustments, lift reworks, etc. All of these exercises involve some degree of inadvertent compromise, largely unrealized by the engineer. This compromise is what results in our compaction standards not being achieved, and causes construction of problematic fill elements founding our infrastructure. (Read more about the greatest problem and solution in infrastructure.) With SSCE® tools, ESOL removes these assumptions and trial & error exercises resulting in uninterrupted construction control at maximal production, real-time data verification of field optimums and compaction states, and known/verifiable compacted strength and stability properties. |